Jacob Deva Racusin is the Director of Building Science and Sustainability at New Frameworks, a Vermont-based worker cooperative committed to building kinder. The practice is dedicated to ecological and social responsibility, including the health of a building’s occupants and those who construct it. New Frameworks is built on inclusivity, and committed to challenging the stigmas of modern construction. The local working landscapes and sustainable agricultural initiatives that fuel their plant-based building solutions are as much a part of their design-build process as their clients.
In addition to energy retrofits and new construction, New Frameworks manufactures a prefabricated straw-bale panel system to scale-up natural building production. The panels form the base unit for their accessible dwelling units (ADUs), called “The Cabañita,” which launched in 2021. New Frameworks is continuing to grow (they’re hiring) while keeping their impact soft.
I had the pleasure of talking with Jacob about his journey to New Frameworks, and all the lessons he’s learned as a pioneer of natural building. Jacob is an endless spring of knowledge, pragmatism and inspiration. He and his colleagues are doing incredible work to bring responsible building into reality.
This interview took place in August of 2023. It has been edited for length and clarity.
Tom Negaard: I’d like to start our conversation by asking about your background: how you came to co-found New Frameworks and your history with natural building materials.
Jacob Deva Racusin: My journey started formally in 2000 when I purchased some raw land. I started a family very young, and had been in the sustainable agriculture and ag-policy world for awhile. I had a really strong interest in learning how to develop shelter and being more in-touch with that part of the human experience — plus, we needed a home. I got my start by developing a homestead up in the mountains by the Canadian border. The house was a post-and-beam framed, straw bale construction — so my first forays into construction were specifically as a natural builder.
I’ll be honest, I was a performing arts/band kid coming out of high school and was totally intimidated by both the culture and technical requirements of construction. I got a lot of advice like: “join a carpentry crew and learn the trades and then build your house…” but I knew that wasn’t my scene. Part of the interest in working with straw was that the community around it was similarly iconoclast and creative, with an open-hearted and positive culture. That was really supportive and made it a lot easier for me socially and technically. There weren’t many rules; it was improvisatory.
Before I finished the house, I realized I actually really enjoyed the building process, so I started building for others, primarily colleagues. I started with lime-and-earth plastering and then expanded to straw assemblies. That ultimately led me to joining up with Ace McArleton in New Frameworks.
After the recession, we were both getting really frustrated with not meeting our social or ecological mandates — only doing single-family new construction in the eco-luxury market. We couldn’t afford any of our own projects, and neither could our friends. The recession gave us the opportunity to change our business model and create a building performance division specifically on energy retrofits. We started New Framework’s building performance wing and joined forces with Ben Graham to create a unified design-build team.
Through the 20-teens, we became much more focused on high-performance design. At that point, I pivoted from being in the field to more on the design side, focused on energy. Towards the end of the 2010s, we started playing with panels as the industry started to turn its attention toward climate impacts. We had been talking about carbon impacts of materials and carbon storage for about a decade, but it was at that time that a lot of attention started started being paid to the work we were doing.
Describe New Frameworks today. How many building projects are you working on? What is the balance between these new ventures, the ADUs and the panel constructions?
We’ve now grown to 20 people (as of August, 2023). The company has a few different nodes. There’s the design team, the build team, a building performance team, a panel production team and an admin team. The teams are fluid — I was offloading a wood fiber insulation last night.
The build side is shifting. We’ve been partnering with other builders to assist with our large, custom residences while we pivot more of our focus to the panels. Our ADUs are, right now, being developed on a custom order basis as we juggle a handful of projects in different phases.
One of the things that came out of reading your report on straw construction was the importance of quality control — how crucial the assembly of these materials is to their performance, not necessarily the materials themselves. You call it out as a barrier to biomaterial adoption, what other barriers persist today?
I can speak to straw because that’s my basis of reference, but it absolutely translates to other ag-residues (e.g. hemp). There were two major barriers when we started: one was establishing the market — letting people know this was even an option and dispelling mythologies around straw (included its durability, architectural value, performance and the climates it could handle). The other half was developing best practices — applying building science and physics.
Paul Lancinski was one of the pioneers of developing early straw bale details in the ‘90s for cold climates. His work, along with that of Mark Rosenbaum and John Straube, built the base for a wave of research over the last twenty years that established published results that our cold-climate straw construction could stand behind. These projects and papers prove that these are actually incredibly resilient and functional materials.
The challenges we are seeing now are more about market regulation and scale of manufacturing. We had spent about a decade, starting in 2006, creating a series of natural building curriculum to do workforce development and get younger people excited about this type of building. What we saw in that decade was a massive decline in the trades writ large, let alone straw construction. Part of our pivot to panels was an effort to get more straw into buildings without relying on custom, in-situ construction. Our biggest challenges are the regulatory barriers and economic/social aspects of scaling rather than initial pioneering of innovative concepts.
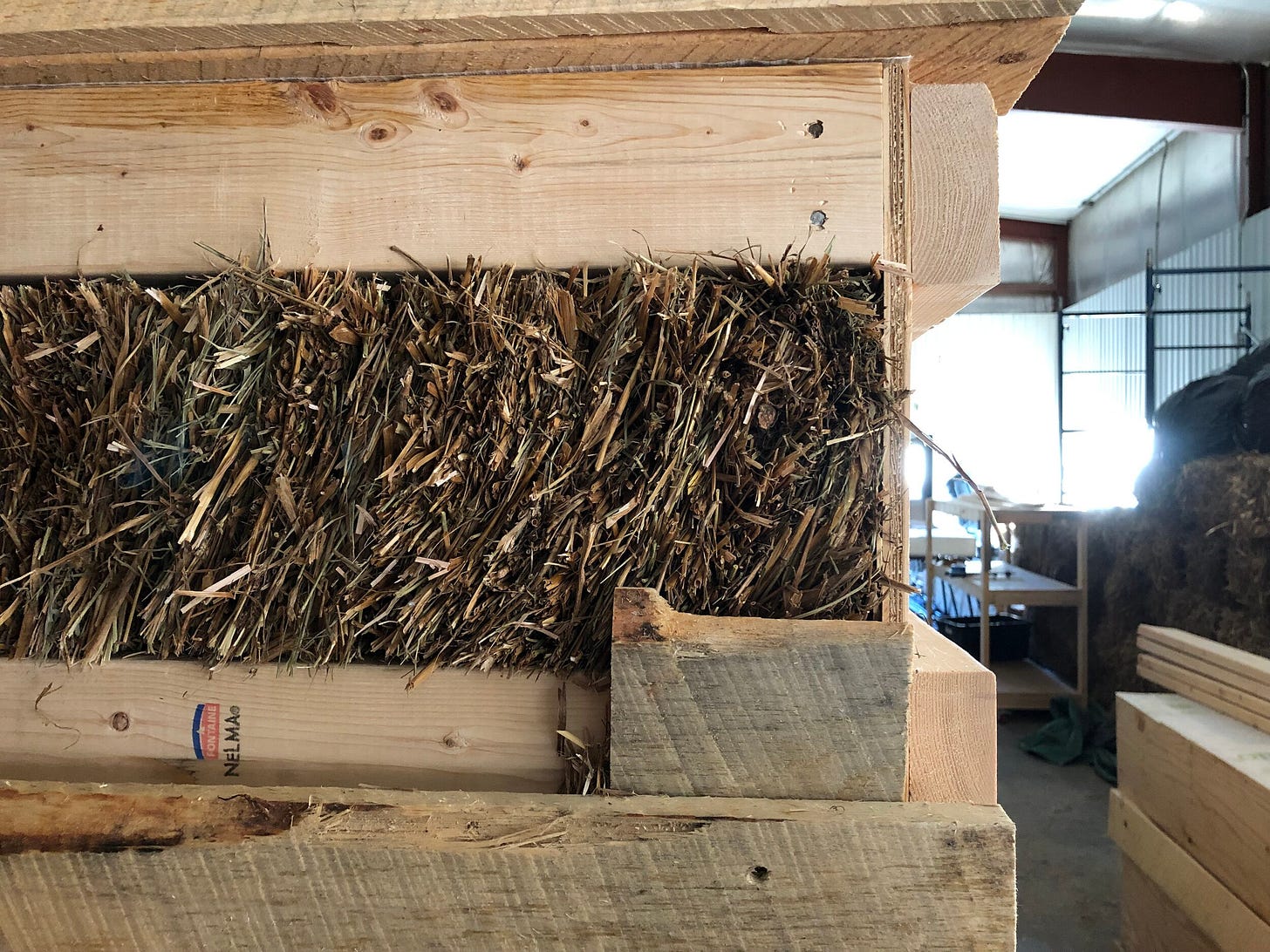
On the topic of sale, one of New Frameworks’ blog posts details your goal to grow via collaboration and engagement instead of the industry-standard silo. Can you talk about what you have learned from scaling up while upholding your multidisciplinary approach?
It’s been really humbling and inspiring. The fact that we have market demand for mid-rise, multi-family urban housing using straw panels that we are not able to immediately meet shows us that our ideas are scaling. I was not expecting this rapid of an uptick.
The scaling of ideas, mission and values has been thrilling. Part of what is reflected back at us is not purely an interest in the technology, but in the regional relationships, the economic relationships and the stories of where these materials are coming from. That holds value in a way that I had not seen before outside very small niches.
We are much more interested in a form of scale that better matches the pattern that we have been working with, which is a much more horizontal. The model we’re pursing with our panel development is not to grow to become the panel provider for the Northeast; it’s actually to create a replicable model and develop a network of cooperatives that can share technology, resources, investments, burdens and benefits of the R&D testing that will be required. It should follow a nature-based resiliency model so that, if one of these companies goes down, it isn’t as if straw panels no longer exist. If we are really talking about up-cycling resource flows and interrupting the carbon cycle with buildings, that transcends a given product or technology; it’s systems-level approach to how we organize building materials.
In an environment when we are seeing increasingly high volatility in agriculture and forestry outputs from climate change, our business structure has to allow for modularity and flexibility. The panels could adapt to whatever agriculture residue is most available. When we’re one forest fire or flood away from losing a crop yield in a given region, that’s volatile. Having a brittle supply chain built off of one large manufacturer and supply base is not the model we want to see, even if that direction would put more straw into buildings.
I keep coming across this tension between the understanding that we need to act fast in changing our ways and the realization that rushing might lead us to skip-over the essential relationships that we need to build with these places, people and materials. Does this resonate with your experiences?
It is an absolute tension. The urgency around needing to act quickly is a critical motivator in compelling all of us, including myself, to continuously challenge our limiting beliefs and the structures within which we are organizing. For example, that’s why we went to panelization; it’s the fastest way to reach the market, prove our concepts and get straw into buildings. But, to your point, that can’t come at the expense of diligence or the core values underlying the motivation in the first place.
Speaking from the mechanical side, the thing that makes me more concerned than anything is seeing policies from well-meaning and decently informed folks pushing for solar panels and heat pumps without any real consideration for load reduction. It seems like a classic example of rushing to this technology to solve a problem without looking at all the relationships.
You can’t skip the relationships; that is the work: developing networks between forestry groups, agriculture sectors, market development groups and the consumer side. Straw panels are like one mushroom popping out of the ground. It’s really the mycelial network of relationships between all these different stakeholders that allows that one mushroom to grow. The technology is seductively fast, but it falls down quickly when it’s not built up with the stronger network of your industry.
I’m wondering if you could speak about your push to reduce toxicity in buildings and the conditions of construction.
Yes, totally, it’s pretty foundational to our work. Our philosophy is that ecological and social justice/health are not separate; they’re inextricably linked. Some of those impacts are more immediately seen within humans versus larger ecological systems. The folks that are fabricating these panels, firefighters putting out these buildings when they burn, as well as workers handling waste during remodeling or demolition, all have direct human exposure and risk based on the toxicity of the materials. We, as builders first and foremost, hold that pretty close to heart, but I can see those risks magnifying up through ecological systems.
I’ve been beating the drum around carbon for a long time now, it’s been a primary motivator and concern for my work. But it’s so easy to have the carbon goggles on, and use them when making crucial material decisions. Looking at material differences outside emissions really matters.
The tension that I often feel in the space is how difficult it is to “do the right thing” while still hitting all the standards and structures (that are there for good reasons) created for petrochemical products. It is structurally unfair in terms of what it takes to bring these novel or innovative materials into legacy industries of power. All the forces around the economic and regulatory factors that govern the real-world evolution of a raw material into a fully-developed product, ready for scale, are such that petrochemicals are cheap. They’re cheap for a reason: our industry and economy has been built upon them being cheap and accessible. That’s a choice made by humans, and we can make other choices.
The exciting part now is that I can make arguments from the standpoint of toxicity, climate-impacts, biophilia, working landscape conservation, and regional economic development for the use of local wood and straw. When firefighters are arguing against the use of plastics in buildings because of toxicity, it’s very different from an environmental scientist’s academic argument. I feel like we are standing in the middle of this collision between these old 20th century structures that were not designed for these (ethical and ecological) values and technologies with a market that says, “we need these product solutions now.”
It seems to me that one big reason why these conventional (toxic/ petrochemical) materials are as economical as they are is because the externalities are unaccounted for. Does this ring true for you?
Two anecdotes come to mind that reflect my experience with this dynamic. Before I came to building, I worked in the agricultural space for a number of different farms. One of my bosses, after encountering headwinds with their organic agriculture initiative, explained:
“We need to grow food that’s healthier, better for the farmers, gentler on the land, looks as attractive, tastes better, is more nutritious and costs the same without using any of the petrochemical-based fertilizers, pesticides or herbicides at our disposal. And if we fall short on any one of those markers, we are deemed a failure.”
That landed heavily for me as a young person. I see that exact same dynamic for all of the women, non-binary and people of color folks within our team. They have to be smarter, faster, more respectable, better performing, excel at every single marker and do so with way less social privilege that I’m afforded. It’s the same pattern, the same structure, it just materializes in different forms.
In my building technology anecdote, I was presenting our work at a materials conference and a major manufacturer of lower-carbon, lower-toxicity foam structural panels was giving me grief that our products were cute but would never scale. I remember thinking that, while he was probably right over the next five-to-ten years, let’s just name that it has become, not only ubiquitous, but essentially required that we insulate urban buildings with petrochemical fuel. This is not a technological problem. Why is it that this was not only allowed to exist, but become essentially requisite: to use toxic fuel to clad our buildings? That’s what externalities look like. It’s a combination of externalities with the literal billions of dollars in tax subsidies that you, me and our friends are providing to the petrochemical industry for the development of their products. If we had a fraction of a percent of that go towards biomaterials, imagine how far down the road we would be in making some of these transitions and even having real options to consider.
Jacob, I really appreciate you work and could talk endlessly about your efforts. Thank you for fighting the good fight, and inspiring us with your research, wisdom and work on the ground.
My pleasure, Tom.
Epilogue
Since our talk, Jacob helped organize and host the Northeast Bio-Based Materials Collective last November in Boston. The inaugural Summit brought together over 60 regional, bio-based experts to discuss the following prompt: How can regionally produced renewable building materials be brought to market, at scale, across the Northeast of North America? I hope to interview Jacob again in the near future about his takeaways from this pivotal event. The proceedings and presentations of the Summit can be found here
For more information on New Frameworks, please check out their website.
Please consider an alternative low-Earth-impact construction:
> Pitch deck, Breakthrough https://alaskaappliedsciences.com/wp-content/uploads/23-Nov6-Breakthrough-ThinShellConc-Pitch-AASI.pdf
> Short Answers, Breakthrough https://alaskaappliedsciences.com/wp-content/uploads/23-Nov13-Breakthrough-ShortAnswers.pdf